Brave New World
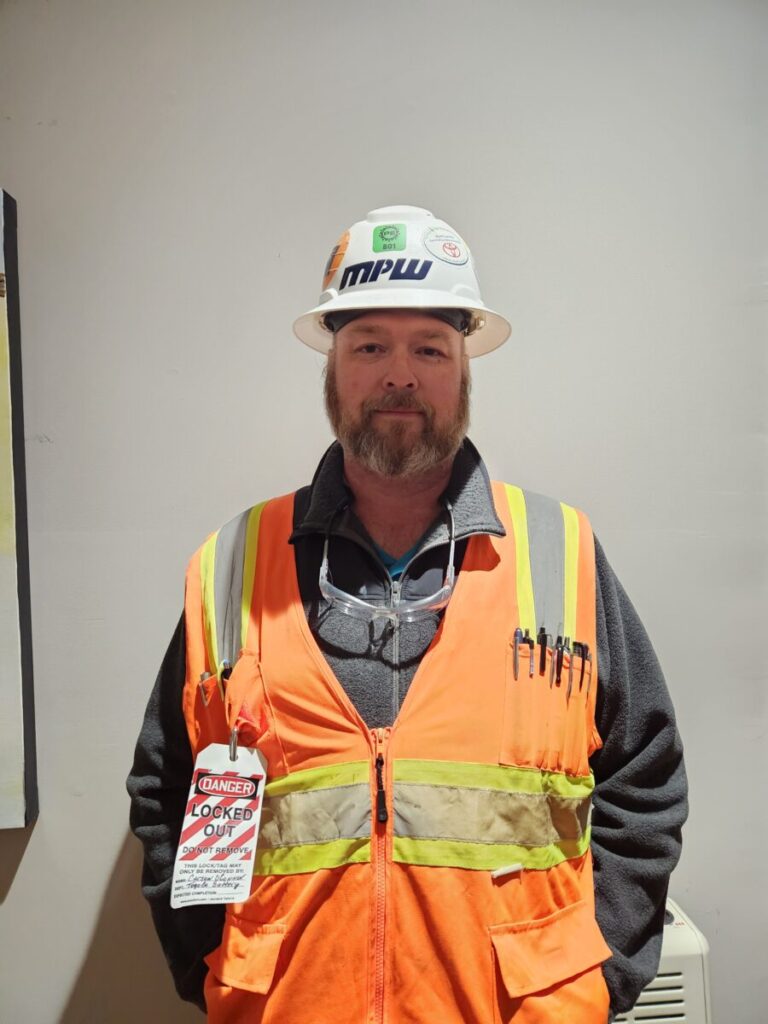
Many managers can rely on mentors and seasoned colleagues for advice and guidance when something unexpected arises or if a procedural change is necessary. In the brave new world of electric vehicles (EVs) and battery construction, a manager may only have personal intuition and experience to keep the project moving forward and the customer supported.
“Tesla’s battery looks like a big D cell, the Toyota battery is flat and looks like a silver cell phone,” said Senior Project Manager Carson O’Connor. “The circle of people we can talk to about the technical production methods is exceedingly small. It is a huge challenge for support, and we must Evolve as a company while we learn the job.”
O’Connor said the projects team group is dedicated to advancing the internal knowledge of the different production methodologies. “Our team lead by Chris Walden and supported by Kevin Mitchell, Mary McCarty, Dave Fopma, and me are leaning on each other for this technical knowledge,” he said.
The automotive industry is in a “big flux” because of EVs and battery plants, O’Connor said. “When you get into proprietary battery production for the different companies, the challenges begin. How each company manufactures its product is vastly different.” He explained that Tesla has one large single production machine that does everything and takes up an entire room. Toyota allocates everything to smaller machines that each complete a specific process. They’re all linked together in one expanded production module.
O’Connor said current and potential customers are understanding that MPW is at the forefront of EV OEM, battery & mega cell power storage production support. “Our competitors don’t do what we do right now,” he said. “Our name is out there in the EV and battery world as ‘Hey, MPW has the experience, technical knowledge and can help us become more efficient and effective.’”
O’Connor began in the automotive industry straight out of high school. “I graduated in 1992 and I went to work at the Nissan plant in Smyrna, Tennessee on the janitorial crew—cleaning the paint lines, restrooms, mucking out a wet system scrubbers and wastewater pits, changing robot covers, all the basic jobs that MPW performs at many customer sites,” he said. O’Connor soon advanced to the assembly line, where his first task was a 12-hour shift, and he had 52 seconds to install two wheels on each passing vehicle.
“That perspective helps when you’re looking at these projects,” O’Connor said. “It helps to know what it’s like to muck out a sludge pit or setting up production support processes. When you’re asking team members to do something like that, you can detail out what you really need to look for from a base line perspective.” It especially helps new team members to relate to their manager about the job and places them more at ease when they understand you have performed these tasks and have an understanding from their point of view.
The senior project manager position takes every aspect of management into account. “It’s a very multi-faceted position and it’s evolved and changed over the years,” O’Connor said. The management process usually begins with MPW receiving an RFP or RFQ from the customer, and then scheduling a walk-through of the job site or an online discussion.
O’Connor said, “Once we go through and gather the technical data, we engage multiple internal MPW parties on what and who we need” (including HR recruiters, purchasing, legal, sales, IT, etc.). He said each region has its own support requirements just as each project requires specific equipment and labor.
O’Connor also contacts the regional safety team member for a safety walk down on the project and makes sure all avenues are covered. And then it’s a matter of putting schedules together, timelines, ordering supplies, equipment coordination, legal reviews, labor support and customer progression updates.
Safety is first and foremost in all aspects of the job. “It’s everything that we can do to recognize and eliminate the hazards,” O’Connor said. “It is looking over the job before we do it and assessing what is needed before we start. We talk about how to mitigate hazards when we see them and make sure each team member understands ‘Stop, Call and Wait’ if they have any question or concerns.” Everyone is encouraged to ask as many questions as possible.
O’Conner said human beings are repetitive at heart and it’s easy to fall into doldrum routines, but on projects especially construction sites your head must be on a swivel. “Read every sign every day, look out those windows and around corners before you proceed, because something could change at any moment,” he said. “Change happens hourly and daily on every project, being flexible and motivated for change makes MPW successful.”
O’Connor said aspiring senior project managers need to understand the amount of travel involved with the position. “It can be a very tough lifestyle for a person to be away from home and family for extended periods of time and not knowing exactly when you can return home,” he said. “We try extremely hard to swap out projects and relieve each other whenever possible for a short stretch to return home.”
But the team members understand anyone may be called at moment’s notice to pack up, catch a plane or hit the road for anywhere in the US. “With Tesla, even though it’s a long-term site, only one of the project team lives in Texas, that’s Dave Fopma,” said O’Connor. “Mary lives in Michigan; Kevin and I live in Alabama. That’s why home times are especially important, and I spend mine with my wife, Mitzy, and my daughter, Keegan.” “For 30 years I’ve been going down this road of learning, growing personally and professionally, gaining knowledge and wisdom as I go, and I really have enjoyed it because of the ever-changing landscape of the automotive world,” O’Connor said. “To me, the automotive industry is really the frontline of technology because every automotive company is looking for the next edge to gain market share.”