MPW knows innovation and automation are the future of industrial cleaning, and so do manufacturers and utility companies.
So, it should come as no surprise that MPW is proposing the installation of water-jetting robots at customer facilities.
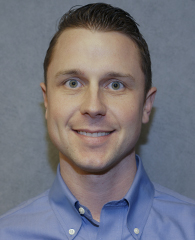
There are numerous advantages to replacing manual water jetting with automated systems, according to MPW Electrical Engineering Supervisor Robb Spangler
“The manual process is physically demanding,” Spangler said. “The equipment weighs 10 to 15 pounds. PPE includes a full blast suit, which is also heavy. And jetting at 40,000 psi, the water comes out at up to 150 degrees, which makes the area even hotter. Our technicians do a great job, but they’re human and they get tired.”
Spangler said in addition to human exhaustion, the robot eliminates the potential for water-jetting injuries, which can result in hospitalizations.
“We’re determined to make our work environments as safe as possible, and automation eliminates a substantial amount of risk,” he said. “The robot doesn’t get tired, it doesn’t get too hot and it doesn’t have to adjust to steamy conditions. So, in addition to being safer, the robotic application improves efficiency.”
Spangler said consistency is another benefit. In recent tests, robotic cleaning sessions are identical nearly 100% of the time.
Reduced labor cost is also a factor, Spangler said. The automated system eliminates the need for the water jetting technician as well as a safety watch who usually alternates duties with the person operating the equipment.
MPW recently filmed a demonstration as part of its own research and development. The team is analyzing the speed and quality of the cleaning and contrasting those results with the current manual water jetting techniques used at a customer’s automotive manufacturing site.
Spangler said MPW customized the robot to clean fixtures for the front bumper of an SUV. These fixtures travel through the plant’s paint line, then into ovens that dry the paint. When paint builds up on the fixtures, it can create errors in vehicle assembly, so the fixtures must be water jetted at 40,000 psi before they can be sent back to the line.
In the demonstration, MPW has designed and installed a customized attachment with nozzles specifically chosen to clean the bumper fixtures. Spangler then programmed the robot’s spinning water jet for the task.
“At one site we might have 10 different kinds of fixtures,” Spangler said. “We would program each fixture into the robot. The robots would be permanent once they’re installed at customer sites, but certainly there are other water jetting applications for other customers — and not just automotive facilities.”
Spangler said MPW’s analysis of the robots reveals impressive data. “We already know we can double the quality of clean, but we can also adjust the speed of the cleaning to conform to how the customer wants their fixtures,” he said. “We will present significant cost savings to the customer, in addition to advancements in efficiency and safety. This is the future of water jetting in facilities.”